Duramax LML vs. LMM Engine Differences
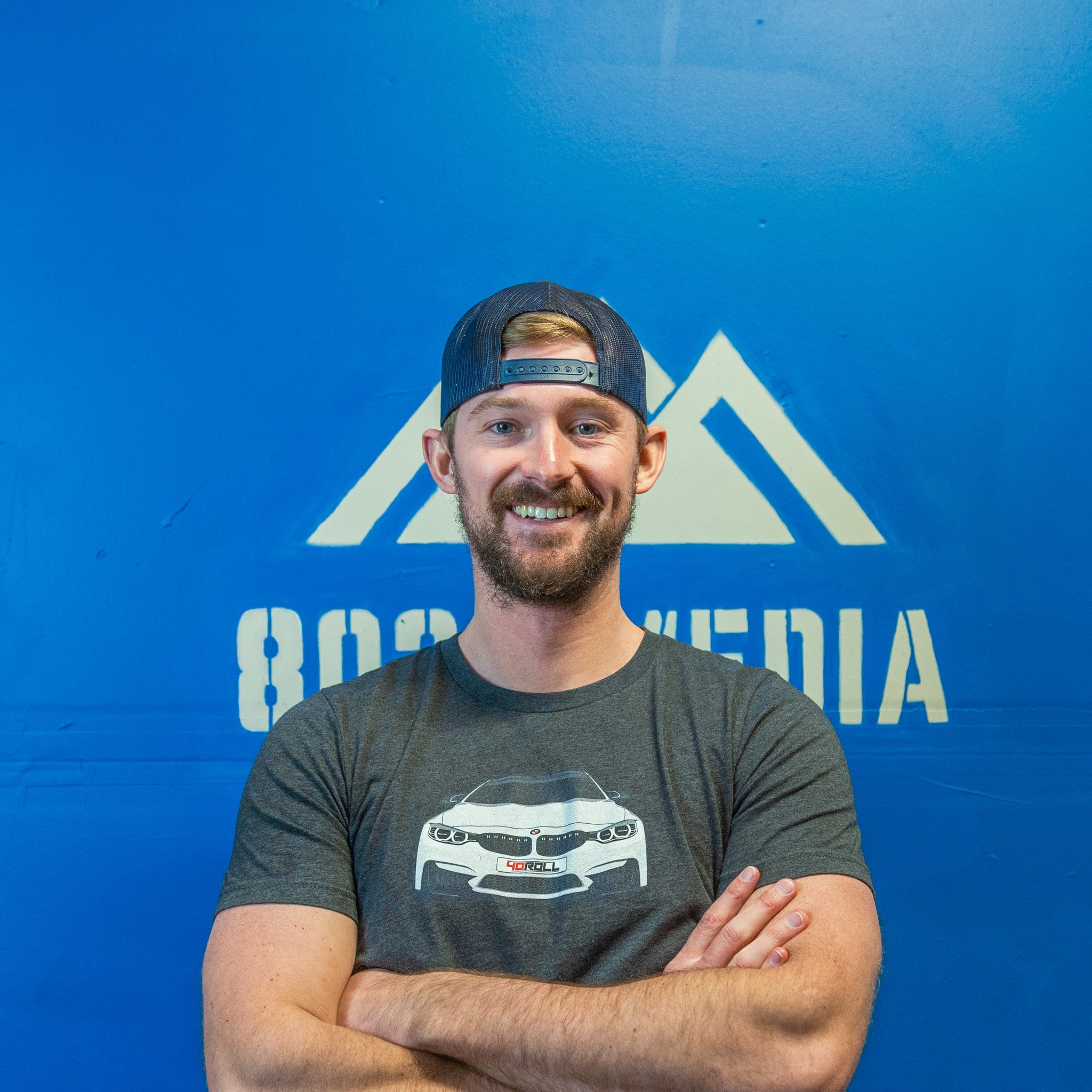
Meet Jake
Jake is a founder of 8020 Media and has been creating automotive content online since 2017. He has been the lead writer for Chevy Trucks and has transformed it from the old and outdated site it was into what it is today. Jake creates a ton of GM related content for the 8020 Media YouTube channel and specializes in Duramax and Vortec information but has a wealth of knowledge across all GM cars and engines. Jake believes the L5P is the best diesel on the market today.
The LML engine got a major overhaul in 2011, compared to the previous LMM Duramax engine. It featured nearly 60% freshly designed parts, only leveraging a portion of the previous engine design.
Up to this point, all of the previous Duramax’s had some internal weaknesses and common problems with bending rods and cracking pistons. The LML engine addressed these issues with strengthened internals and a stronger block.
Furthermore, some major changes were made to the injection pump – switching from the CP3 to the CP4.2, which turned out to be a terrible idea. And lastly, the engine got some fancy new emissions equipment. So let’s jump in and discuss in more detail the changes on the LML vs. LMM Duramax.
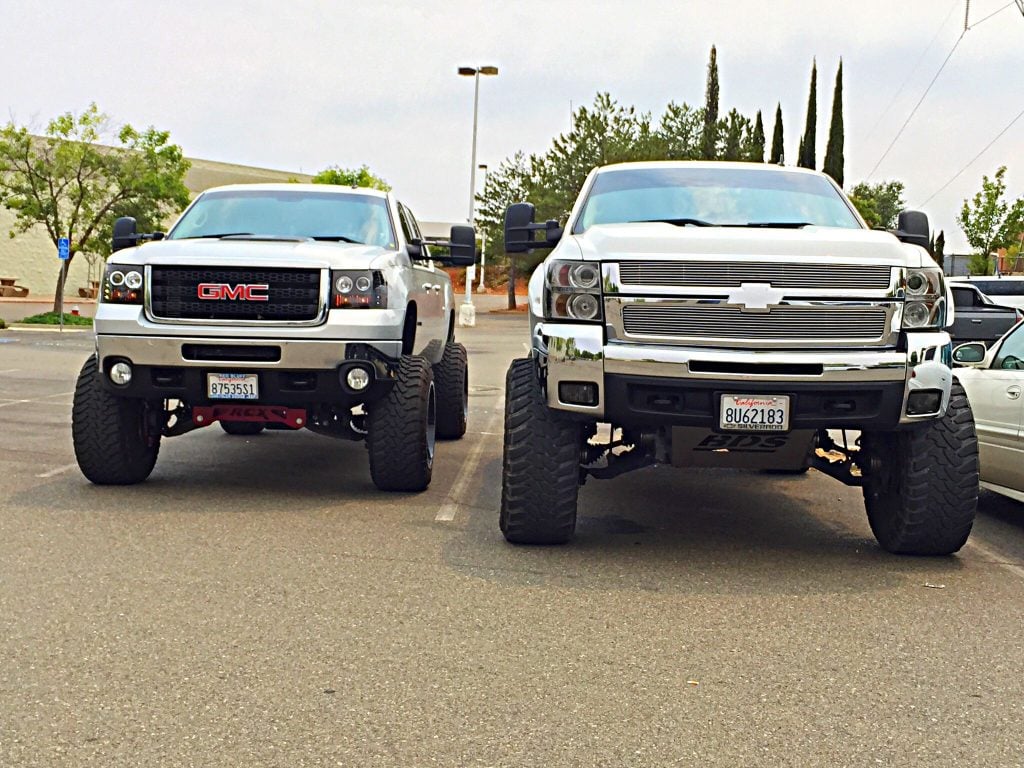
Block, Rods, & Pistons
First, the engine received a strengthened block and improved main bearing to improve on previous weaknesses. Additionally, the rods and pistons were both strengthened while actually being lighter, creating a lighter rotating assembly. While the rods and pistons are both made similarly and out of the same material as the LBZ/LMM rods and pistons, the piston wrist pins had modified ends for more support and the rods featured a cracked cap design. All of these changes significantly improved the durability and strength of the rods and pistons over the previous versions.
With the improved rods and pistons and lighter rotating assembly, cracking is no longer a common issue as it was on LMM and LBZ models and the internals can now handle up to approx 700rwhp without any issues.
Injectors & Injection Pump
The LML included an advanced injector design, capable of 30,000psi of pressure compared to 26,000 on the LMM. The increased pressure capacity allows the engine to produce the significant power.
To support the higher pressure injectors, the LML was fitted with the Bosch CP4.2, upgraded from the previous Bosch CP3. Despite the upgraded injection pump, it actually flowed 20% less fuel than the CP3, creating problems with performance modification and tuning. Additionally, the injection pump does not take well to contaminates and poor lubrication, causing a myriad of potential problems which we’ll cover later on.
DPF & a 9th Injector
The DPF regeneration process was overhauled by adding a 9th injector in front of the diesel oxidation cat which is located within the turbo downpipe. The 9th injector receives fuel from the CP4.2 and injects it directly into the exhaust system. This removed the oil dilution issues with the LMM engine and increased the regeneration intervals.
DEF & SCR
Selective catalytic reduction was added to the engine, which injects a special fluid, known as diesel exhaust fluid into the exhaust system. The exhaust fluid creates a chemical reaction which convers nitrogen oxide (the bad stuff) into nitrogen, water, and carbon dioxide. While these systems further complicate the broader emissions process, they actually improved fuel economy by about 10%.
The drawback is that you now have to also fill your Duramax engine up with diesel exhaust fluid on a regular basis, although it is relatively inexpensive and offset by the fuel economy gains.